As a homeowner, one of the best ways to learn about plumbing services is through a case study. Being able to see a real project from beginning to end helps to understand the scope of the work and how to judge between different plumbers’ quality of craftsmanship.
Today’s featured project was at a typical central Plano home near Custer Road and Park Boulevard. Built in 1971, this 1,800 square foot home had been tastefully updated. It has four bedrooms and two and a half bathrooms with an attached garage and natural gas supplied to the residence.
Houses built around this time in central Plano tend to share many things in common. Plano was going through a residential construction boom because Dallas residents were looking for practical, affordable houses for their families that were still close enough to the city.
Builders known for their economy of scale like Fox and Jacobs installed thousands of houses just north and south of what is now called the President George Bush Turnpike.
Today’s case study is a perfect example of major plumbing repairs in Plano that some homeowners will face.
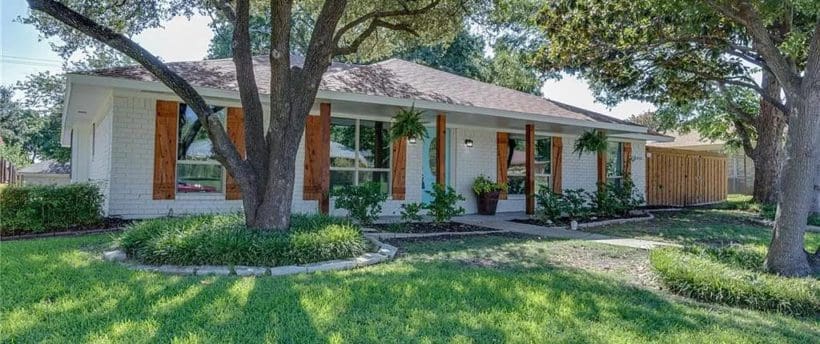
Calling a Plano Plumber for a Clogged Drain
When Legacy Advocates booked this call, we initially were going out to address a stopped-up bathroom drain. This is common enough. But there were some tell-tale details that hinted at the bigger problems that lay beneath.
The age of the home was one factor that hinted at a bigger plumbing repair. The early 1970s was before PVC pipe came into the market. The best drain pipe material widely available at that time was cast iron. While it is very robust and reliable when first installed, cast iron inevitably rusts out and deteriorates with age. It’s not a matter of “if”… but “when” cast iron drain pipes will need to be replaced.
This wasn’t the first time a clog had occurred either. This home had a history of drain backups, especially in this one bathroom. A history of repeat clogs on a cast iron sewer line greatly increases the chances that significant issues exist.
History of Past Sewer Repairs
In addition to repeat clogs, there were also repairs that had been made to this home’s sewer pipes in the past. There was at least one time (the homeowner was aware of) that a drain pipe under the slab had been dug up and fixed.
The way cast iron deteriorates, there usually isn’t one clean break that needs repaired while the rest of the system is in decent shape. If a cast iron pipe is broken or deteriorating in one section, other parts of the system often aren’t far behind.
Shifting Slab Foundation
The last clue that there were more extensive issues was that the homeowner also told of a shifting foundation.
Foundation issues are common in Plano due to the expansive clay of north Texas soil. To make it worse, shifting slab foundations have a strong association with broken pipes under the home.
Sometimes, the shifting foundation causes a leak because the movement itself breaks the sewer line. Other times, the water leaking out of a deteriorated drain pipe is what causes the foundation movement by expanding the clay soil.
The Discovery of a Cast Iron Pipe Slab Leak
Our company dispatched Kelly, a senior Legacy Plumbing technician to address the initial issue of the clogged drain and to inspect the cause. Kelly started by attempting to clear the clog with his drain machine.
A Clogged, Broken Sewer Pipe
It wasn’t long after starting to run the drain cleaning machine that Kelly ran into some issues. The powerful sewer machine began to bog down as the end of the cable began to bind up in the drain pipe.
After several attempts to unsuccessfully get through, Kelly removed the drain cable and examined the end. Unfortunately, it was packed with hard Texas clay mud. Kelly said:
“I ran a cable and wasn’t able to clear the stoppage because my ⅞” cable would drop into what turned out to be the trench rot… it was a hard stoppage from a deteriorated pipe.”
After trying unsuccessfully several times to clear the stoppage by machine, Kelly knew there was an issue that needed to be looked into further.
The Sewer Camera Inspection
The next step was to inspect the pipe with a camera and see if more of the problem could be visually identified:
“Once we figured out that I couldn’t clear it – that my cable would drop down into the soil – we inspected the line with a sewer camera. … As my camera went down the line, I could tell that it would drop in a certain area where it shouldn’t.”
In other words, the bottom of the old cast iron pipe had completely deteriorated away! While the camera would normally skate along the bottom of the pipe, when it neared the blockage it just dropped down into the dirt under the pipe.
After discovering the underlying issue behind the repeated drain clogs, Kelly discussed the situation with the homeowner and what the possible options were.
Options for Cast Iron Sewer Repair
There is almost always more than one option to repair a damaged sewer line. From just replacing the single broken spot all the way up to a full drain pipe replacement.
At Legacy, we prioritize giving options and walking the homeowner through the pros and cons of each so that they can make the best decision for their home and their family. In this case, there were two main options that the customer was considering.
Spot Repair of a Cast Iron Sewer Line
A spot repair involves accessing the portion of the pipe where the known issue is, cutting it out, and just replacing that section. Sometimes this is an option, but if the deterioration of the pipe is extensive, it is better to replace vs. repair a small section.
The homeowner previously had a spot repair completed near the current break. This provided further evidence that the entire cast iron line was deteriorating.
Full Under-Slab Drain Pipe Replacement
Instead of trying to fix the bare minimum (or even a larger section of the system) the homeowner was leaning toward replacing the entire drain piping system at the same time. This would get rid of all horizontal cast iron drain pipe and replace it with new PVC drain pipe.
With everything under the slab replaced, the whole house would flow smoothly – eliminating clogs and taking care of drain problems for the foreseeable future. Eventually, this was the option decided upon:
“We submitted a quote for the spot repair and for the whole house repipe. … Ultimately, he decided he wanted to repipe the whole house.”
Laying Out A Drain Pipe Reroute
Another significant advantage of replacing everything at once is that it opens up more possibilities. The new piping doesn’t have to follow the exact same path as the old pipe.
Since all of the sewer drain system under the house was being replaced, Kelly was able to design the new system so that the kitchen, laundry, and nearby half bathroom drains were rerouted through the side yard. This minimized the tunneling necessary – reducing excavation costs and making the system more serviceable for the future.
Digging the Tunnel For Cast Iron Pipe Replacement
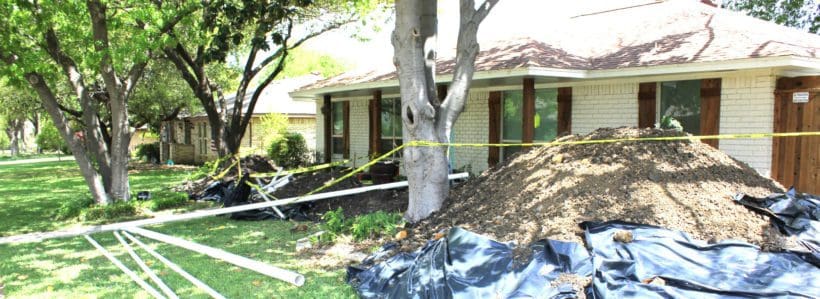
After the homeowner decided to move forward with a full drain system replacement, Kelly got the process started. Legacy does things “by the book”, and this job was no exception.
Kelly started by pulling a permit from Plano’s building department. This means that a city inspector would come out once the new piping was installed and verify that the installation passed the state of Texas and local plumbing code requirements.
Setting Up A Tunnel and Trench Excavation
Kelly coordinated with Legacy’s excavation crew to get the tunneling done under the house as well as the trenching through the yard. A total of 68 feet of tunnel was dug under the foundation and 85 feet of trench was excavated in the yard. This took the excavation crew about two and a half days to accomplish.
Legacy’s excavators dig everything by hand. They work neatly and quickly – setting all the excavated dirt on plastic and putting aside any moved landscaping for easy replacement. The tunnels also have safe dimensions. The access pits are a full 3’ x 3’. The tunnels themselves are dug squarely with plenty of room to work safely and efficiently.
Replacing the Old Cast Iron Pipe with New PVC Pipe
The process of replacing drain pipe under a house via tunnel is both labor-intensive and requires a high degree of skill. Kelly and his apprentice were the perfect team for this project.
The old piping was carefully disconnected from where the pipes rose up through the slab to serve the home’s tubs, toilets, sinks, and etc… A few of these connection points were encased in concrete that had to be carefully chipped away first. Once the cast iron was removed, they started with the installation of the new pipe.
Connecting to Old Cast Iron Pipe
First, all of the vertical pipe connections had to be cleaned and prepared so that they could be adapted to without leaking. For these connections, Kelly used stainless steel band reinforced couplings which were then torqued down to the correct specifications.
Some other companies purchase a cheaper version of this adapter coupling that works in the short term, but provides less resistance to being offset by any ground movement.
Supporting the New Drain Pipe in the Tunnel
The new PVC that Kelly installed was the traditional solid core PVC piping instead of the less-robust “foam core” PVC pipe that is on the market today (which some other companies use.
In order to support that pipe at the proper slope and keep it from moving in the future, Kelly installed steel hangers which were anchored up into the concrete slab. As part of our standard, Legacy installs twice as many support hangers as is required by code!
Slab Leak Repair Testing and Inspection
After all of the new piping was installed and sloped correctly, Kelly had to test his work and set everything up for the city inspection. Legacy coordinates this so that it works for both the city and the homeowner’s schedule – minimizing system down-time.
“First and foremost is communication with the homeowner – letting them know what to expect for the inspection.”
Testing Sewer Repair For Leaks
The testing process for underground drain pipes is often referred to as “hydrostatic testing”. It involves temporarily plugging the main drain pipe and filling all of the newly installed piping with water. In this way, any leaks are quickly made apparent as the water level will start to drop.
Kelly also took photos of all the connection points and piping runs under the slab for the homeowner’s future documentation and for city inspection purposes.
Plano City Inspection
After the city inspector passed the test and the installation was up to state and city plumbing codes, the project was officially “green tagged” and approved to back-fill. At this point, Kelly removed the test and the brand new system was fully functional. All that was left was putting the soil back and finishing the final touches.
How The Slab Leak Tunnel Repair Affected the Foundation and the Yard
At the end of a project of this scope, you might expect a pretty big footprint and some remodeling work. However, Kelly barely had to even go inside the house. The bathroom toilets were reinstalled on new PVC closet flanges. Other than this, all of the work was done from underneath without disturbing the inside of the house at all! No concrete penetrations or dust required.
Engineer’s Slab Tunnel Compaction Report
Just as the impact to the interior finish of the home was minimal, so was the impact to the slab foundation.
The tunnels and trenches were refilled by our excavation crew. In order to minimize future settling, the soil was wet down when being replaced with a special method called a “mud-packed backfill”. In this way, as much dirt as possible was replaced back under the slab.
A drawing of the tunnels was created and Legacy submitted the details to a licensed engineer who wrote a compaction report – assuring the work hadn’t reduced the stability of the slab foundation in any way.
Drain Pipe Trench Backfilling
A similar process was used to backfill the trenches in the yard. With a mud-packed backfill, future settling is minimal. After filling everything back in, the house’s yard and landscaping wall all put back together. Other than where the green grass under the dirt pile had temporarily faded due to lack of sun, it would be difficult to tell that any work of this scale had been done at all.
Having completed many such tunnels over this time frame, Kelly said that it usually takes a couple of weeks during the growing season for the grass to regain its full color and the final traces of the project to completely disappear.
Why Legacy is the Best Plano Plumber For Sewer Repair
Hopefully, this case study answers a lot of questions for what a professional sewer repair or drain pipe replacement should look like.
This was a very typical home to undergo this sort of project. The processes/timelines are pretty representative of the thoroughness and efficiency with which Legacy works.
Drain Pipe Replacement Warranty
Legacy’s tunnel drain line replacements are warrantied for a full 5 years. This warranty is fully transferable to new homeowners if the house is sold. Because it is backed by Legacy Plumbing, homeowners can rest assured that their new drain pipe system will be reliable for many years to come.
Upon completion of the work, we put together our warranty documentation, a completed engineer’s compaction report, and photos of the work performed into a job folder for your personal records.